Ethylene Oxide (C2H4O) Handling
Operator and Environmental Safety – SafeRack has been providing safe, reliable platforms, handrails, and gangway solutions to the chemical industry for many years. From multifaceted fall prevention retrofits to new builds, SafeRack’s priorities are operator and environmental safety while still focusing on creating an efficient and productive solution that allows a significant return on investment.
Ethylene Oxide Chemical Overview
EtO is a flammable, colorless gas at temperatures above 51.3 degrees F (10.7 degrees C) and smells like ether at toxic levels. EtO is found in the production of solvents, antifreeze, textiles, detergents, adhesives, pharmaceuticals, and polyurethane foam.
What is Ethylene Oxide?
Ethylene Oxide or EtO is a flammable, colorless gas with a sweet odor. It’s used as a chemical intermediate in the manufacture of ethylene glycol and also used as a sterilizing agent and fumigating agent.
In the United States, Ethylene Oxide is typically a “tight-fill” (closed-loop) loading operation and is loaded into rail cars via chemical hoses or 3” stainless steel loading arms. Ethylene Oxide, if not handled properly can cause serious injuries and Personal Protective Equipment (PPE) is required. Additionally, because operators are on top of the vehicles during the loading process, fall prevention is essential, not only for safety but increases throughput.
Ethylene Oxide is typically shipped in DOT-105J insulated tank cars with safety valves that meet the DOT specification for the transportation of Ethylene Oxide and other similar commodities.
The rails cars themselves are ~ 9′ outside diameter with an overall length of ~45’ to 60′, with a 6’ x 6’ center opening or off-set opening crash box
Trailers are top unloaded. An extension pipe with two valves is flanged to the top of the trailer. One valve is located at the top, and the other is at the end of the pipe on the bottom for easy access. Trailers should arrive on-site with blind flanges.
All trailers must be equipped with pressure relief valves, and trailers with bottom outlets must be equipped with remote controlled stop valves. Tank truck (un)loading procedures are similar to railcar applications with the trailers meeting established DOT requirements for hauling ethylene oxide or similar cargo. Approved DOT trailers include MC 300 thru MC 312, MC 330, and MC 331.
Ethylene Oxide is regulated by the U.S. Department of Transportation (DOT) and is classified as a flammable gas with the DOT identification number UN 1040.
Do not handle this product until all safety precautions have been read and understood. Best practice loading/unloading includes wearing chemical-resistant clothing, gloves, splash goggles, and respirator at all times to protect eyes, lungs, and skin.
EtO causes skin and eye irritation and is toxic if inhaled. Chronic exposure can result in damage to internal organs such as the nervous system and kidneys. Exposure may also cause genetic defects, cancer, and damage fertility or the unborn child.
Ethylene Oxide is a highly flammable gas and forms explosive mixtures with air. Vapors are heavier than air and may collect in low spots. Because of the potential for violent decomposition, containers of EtO must be properly blanketed with inert gas and protected against fire exposure. In the event of a spill or leak, exit the area immediately. Eliminate heat and ignition sources such as sparks, open flames, hot surfaces, and static discharge. Post “No Smoking” signs.
Only properly trained and equipped personnel should be permitted to unload tank trucks. Operators should wear an approved respiratory protective device, and impervious clothing, footwear, gloves, and goggles.
OSHA Permissible Exposure Limits (PEL) @ 1ppm in an 8 hour day.
Ethylene Oxide is not compatible with aluminum, cast iron or carbon steel, so great care should be taken to avoid contact with these materials. However, galvanized or stainless steel is tolerable with Ethylene Oxide.
Ethylene Oxide Products
Safety Swing Gates
YellowGate – The Original Universal Self Closing Safety Gate
Loading Dock Stairs
Prefabricated IBC, ADA, or OSHA Loading Dock Steps
Skids
Transloading Skids
Mobile Work Platforms
The MP Series is a highly mobile work platform designed to bring the workspace and stability of a fixed platform to a rolling stair mobile unit.
Signs and Signals
Signs and Signals
Railcar Chocks/Blocks
SafeRack’s railcar wheel chocks provide fast blocking of all types of railcars
Lighting
Lighting
Drench Showers
Emergency Drench Showers and Safety Eyewash Stations
Pipe Racks
Prefabricated Pipe Racks Constructed Faster and Easier Than Ever Before
Metering
Metering
Overfill Protection
Overfill Protection
Grounding/Earthing
Grounding/Earthing
Beam Trolley & Lifeline
Fall Arrest Systems for Horizontal Mobility at Heights
Safety Gates
Safety Gates
Drum & IBC Spill Pallets
Drum & IBC Spill Pallets
Truck Spill Containment
Truck Spill Containment
Railcar Track Pans
Railcar Track Pans
Top Loading Arms
Top Loading Arms
Safety Cages
Safety Cages
Portable Access Platforms
SafeRack’s MAUI mobile access units provide secure, adjustable stair solutions for safely accessing elevated truck and railcar work areas, even in the most challenging environments.
Transloading Skids
Transloading Skids
MaxRack Elevated Platforms
Powered elevating platform system for accessing railcars and trucks
Ship & Fixed Ladders
Fixed ladder and steep inclined ship ladders for areas where standard stair length runs are not feasible.
Crossover Stairs
Crossover Stairs
Industrial Access Stairs
Prefabricated industrial stairs and access platforms offer safe, durable, and expandable access with quick, no-fabrication installation.
Truck & Railcar Gangways
SafeRack Truck & Railcar Gangways
Solutions
Below are some of the loading and unloading solutions for illustrative purposes only. Our experts will work with you and your team for a custom solution to suit your needs.
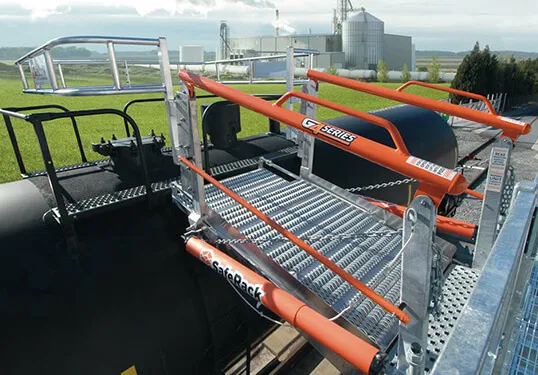
Loading Gangways & Safety Cages
Wide access gangways (48″-60″) are preferable to allow safe access and egress to and from the vessel. In addition, a wider gangway reduces the risk of PPE getting caught, torn or damaged, while improving productivity and safety. Powered gangway solutions allow for hydraulic and pneumatic use, reducing stress and strain on operators.
Each gangway is fitted with a two-rail safety cage for the railcar crash box or a four-rail safety cage for access trucks.
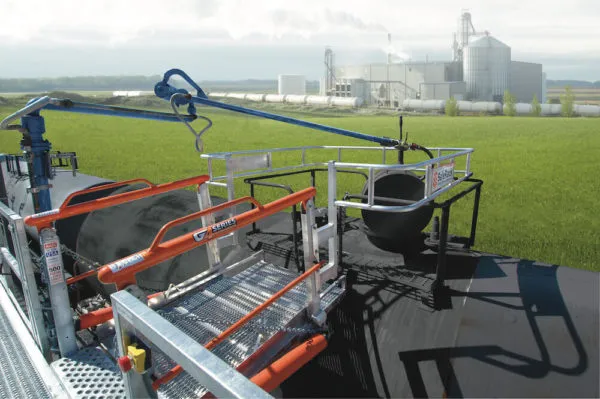
Loading Arms
Chemicals are typically loaded into railcars or tank trucks via boom-supported 316 stainless steel loading arms or chemical hoses with a flange connection. The arm or hose uses a top inlet with a control valve to ensure that it is self-draining after use and is supported along the length of a mechanical loading arm (by-pass arm) to improve handling. When required, a vapor hose can be mounted on one by-pass arm.
When unloading, use of a rigid 316 stainless steel arm with EPDM or PTFE seals or a braided stainless steel chemical hose is typical. Purge lines can be fitted to the arm for nitrogen purging. Additional features such as parking latches with proximity sensors can be incorporated into the total system to ensure the arm is correctly stowed when not in use to prevent rail movement.

Eye Wash/Drench Showers
ANSI guidelines state that an Eye Wash/Drench Showers need to be located 10 seconds or 55’ (16.8m) from contaminants or hazardous materials.
Eyewash stations need to be on the same horizontal plane with no obstructions.
Therefore, we propose installing a standard combination Drench Shower/Eyewash Unit, which will save limited space and fit easily into any work environment.

Spill Containment
Spill containment, such as railcar track pans will be provided at the point of loading operations and are an essential piece of equipment in overall site safety and environmental protection.
Wheel chocks allow for safe access to and storage of treatment chemicals, while spill containment pans utilized at the point of loading operations serve as essential safety and environmental protection tools.
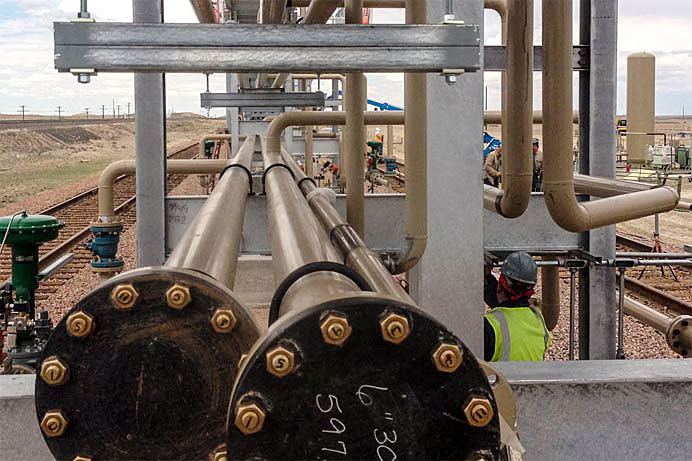
Piperacks
Because chemical plants have pipe runs throughout the facility, ErectaRack pipe racks are pre-fabricated for a variety of pipe dimensions and applications. Because they’re pre-engineered, ErectaRack skips the long engineering and fabrication process, saving weeks, if not months in the installation process.
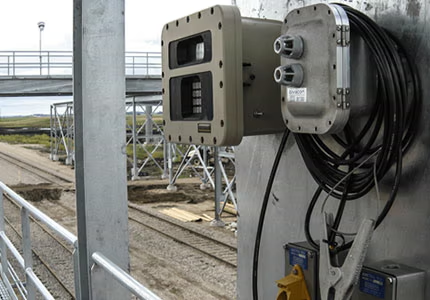
Grounding
Proper grounding is essential when loading and unloading chemicals to prevent static electricity buildup, which can cause sparks and lead to fire or explosion hazards. SafeRack offers grounding systems designed to ensure a secure connection between the transport vehicle and the facility, meeting industry safety standards while protecting personnel and equipment.
Vehicle grounding and bonding — ensure true grounding before product flow is permitted
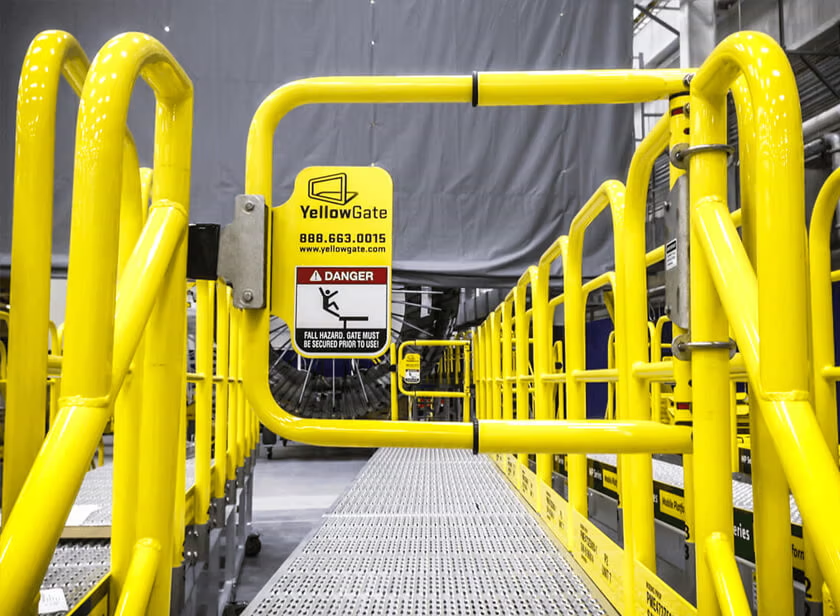
Safety Gates, Stairs, Ladders, & Platforms
Safety Gates will be installed at the top of stairs and any other openings to ensure operator safety.
SafeRack’s line of industrial safety gates is the most flexible product on the market with the ability to span openings between 16” and 36” and is field adjustable with nothing more than a wrench. We also have guardrails, metal handrails, and full-fledged fall protection solutions with customizable options to fit your needs.
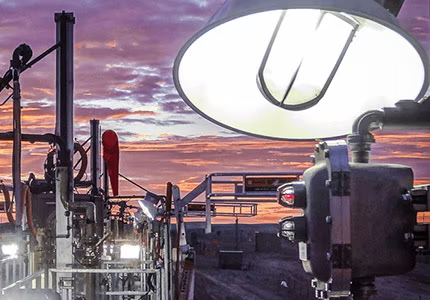
Loading Platform Options
Lighting – General exterior and task lighting to illuminate work and walk areas.
Platform & Canopies – Full platform canopies reduce exposure to the elements and improve the safe and productive loading operation from the operator’s perspective.
Operator Shelter—Depending on your site requirements, consider the requirement of an operator or guard building to keep personnel out of the elements. This can be customized to meet specific site requirements.
Wheel Chocks – SPCC options to allow for safe access and storage of water treatment chemicals.
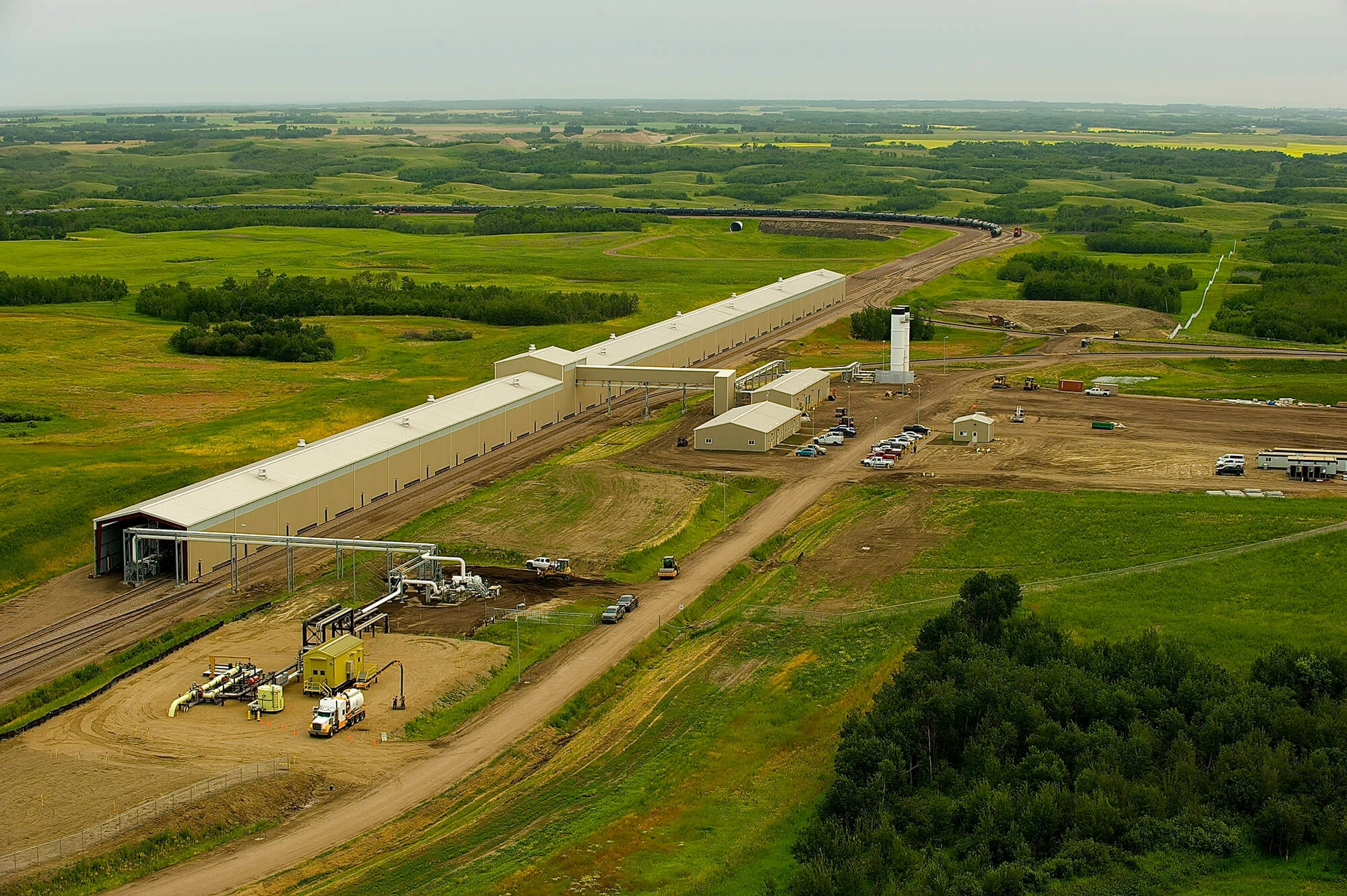
North America’s largest loading terminal
As one of the primary railcar loading points, Hardisty is one of the major crude oil hubs in North America and a major origination point of pipelines that export to the United States. SCS was asked to supply and construct a SafeRack crude oil loadout terminal spanning nearly half a mile. The USD Hardisty terminal can load up to two 120-railcar unit trains per day and consists of a fixed loading rack with 62 railcar loading positions enclosed, separate control, operator, and mechanical buildings, as well as a unit train staging area and loop tracks capable of holding multiple unit trains simultaneously. SCS also supplied and installed boom-supported loading arms with supply and vapor management systems.
Why SafeRack?
The SafeRack approach is collaborative. Let’s call it The SafeRack Way. Over many years, we have amassed a great deal of experience and understanding of the safety aspects involved in loading road tankers and railcars, as well as the behavioral habits of the operators.

Ethylene Oxide
Is your facility compliant with ANSI, OSHA, and local safety codes? We can help!
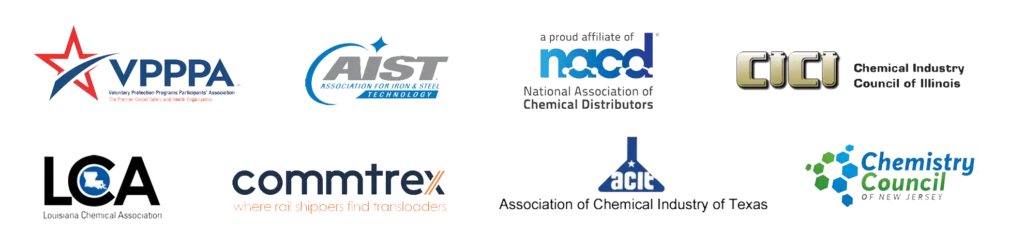
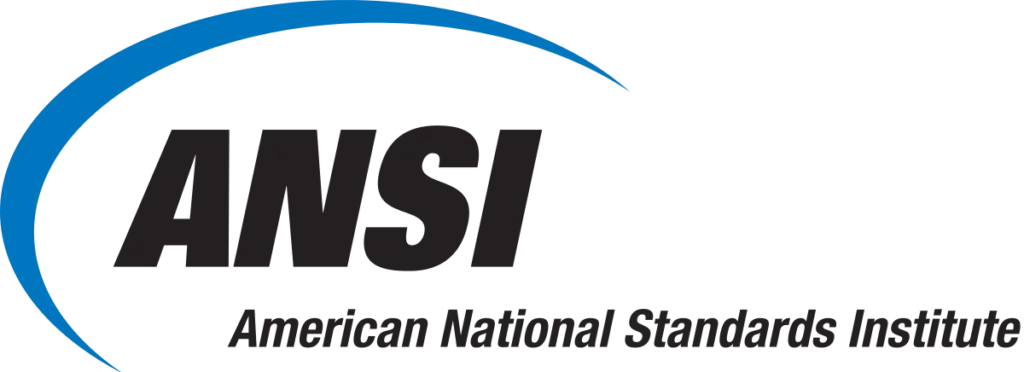
EMERGENCY EYEWASHES / SHOWER EQUIPMENT AND THE ANSI/ISEA Z358.1 – 2014 STANDARD
Following eye contact, you must start washing with water immediately to prevent permanent damage. In the event of skin contact, you must start washing with water immediately to prevent slow-healing chemical burns.
Are you aware that ANSI guidelines state that Eye Wash/Drench Showers need to be located 10 seconds or 55′ from contaminates or hazardous materials and located on the same horizontal plane, with no obstructions? If bottom loading/unloading, an additional shower should be located at grade as well. SafeRack provides the above equipment plus much more needed to keep employees safe and expedite bulk chemical loading and unloading.
OSHA Regulation Experts – Does your existing chemical safety equipment or chemical loading systems meet OSHA’s latest requirements? SafeRack’s professional technical sales consultants are available to meet with your team to make recommendations to keep your facility in front of OSHA’s ever-changing country and region-specific standards and regulations, including lifeline and trolley beam fall arrest systems, metal stairs, and access platforms.
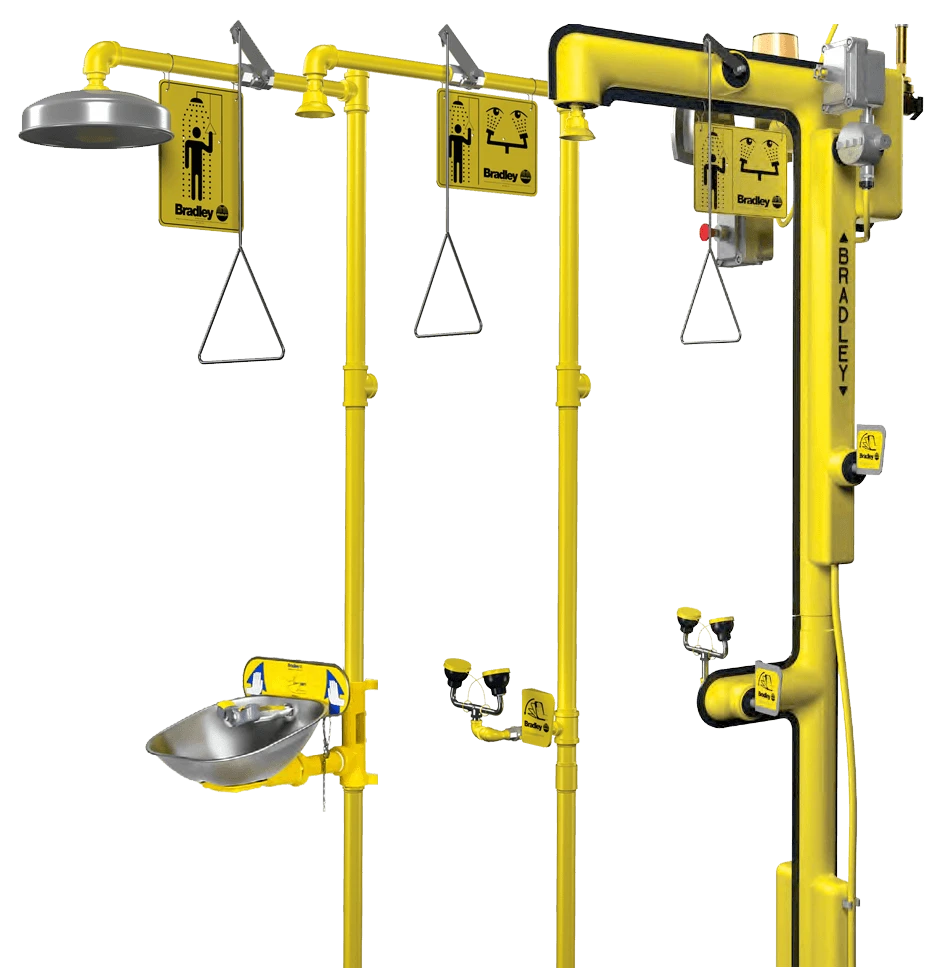
Petrochemicals are made from either petroleum or natural gas feedstock. A wide variety of petrochemicals are created/produced depending on the process.
Synthesis gas (SynGas) – A mixture comprising of carbon monoxide, carbon dioxide, and hydrogen. Common Synthesis Gas is Ammonia and Methanol. Often used for creating Fertilizers and explosives. Synthesis gas is a mixture of carbon monoxide and hydrogen used to make ammonia and methanol. Ammonia is used to make the fertilizer urea, and methanol is used as a solvent and chemical intermediate. Steam crackers are not to be confused with steam reforming plants used to produce hydrogen and ammonia.
Aromatics – Aromatics are hydrocarbons that consist exclusively of the elements carbon and hydrogen. Common Aromatics are Benzene, Toluene, and Xylenes. Often used for creating Dyes, synthetic detergents, fibers, and plastics.The catalytic reforming of naphtha produces aromatics, which include benzene, toluene, and xylene. Together they are referred to as BTX and are predominantly obtained from petroleum refineries by the extraction from the reformate produced in catalytic reformers using naphtha obtained from petroleum refineries.
Olefins – The most reactive class of hydrocarbons tend to crack. Common Olefins are Ethylene, Propylene, and Butadiene. Often used for creating plastics, and synthetic rubber. Chemical plants produce olefins by steam cracking of natural gas liquids like ethane and propane. Olefins include ethene, propene, and butadiene. Ethylene and propylene are chief sources of both plastic products and industrial chemicals. Butadiene is mainly used in the production of synthetic rubber.